製造現場で日々の作業効率が低下し、収益性に影響を与えていると感じていませんか?
多くの工場では、気づかないうちにスペースの無駄遣いが発生し、年間で数百万円もの損失につながっています。しかし、適切な空間活用の手法を導入することで、この問題を効果的に解決できるのです。なぜなら、パーテーションによる空間の最適化や動線分析に基づくレイアウト改善は、大規模な設備投資なしで作業効率を平均20%向上させる実績があるからです。
本記事では、工場スペースを有効活用する具体的な3つの手法と、業種別の成功事例を詳しくご紹介します。これにより、限られた工場スペースから最大限の価値を引き出し、生産性の向上と運営コストの削減を同時に実現できるでしょう。
工場内のスペース活用でお困りではありませんか?
効率的な空間設計で生産性向上を実現しましょう!
工場でよくある「スペースロス」の課題と影響
製造現場において、スペースの使い方は生産性と直結する重要な要素です。しかし、多くの工場では気づかないうちにスペースロスが発生し、それが様々な問題を引き起こしています。工場設備の配置や作業動線の設計は、一度決めてしまうと変更が難しく、その影響は長期にわたって続きます。ここでは、製造業の現場でよく見られるスペースロスの実態と、それが引き起こす具体的な課題について詳しく解説していきます。
作業動線の非効率による生産性低下
工場内での従業員の移動距離は、想像以上に生産性に大きな影響を与えています。製造ラインのレイアウトが適切でない場合、作業者は必要以上の距離を移動することになり、それが時間のロスとなって表れます。実際の現場では、1日あたりの移動距離が必要以上に長くなることで、作業効率が低下する傾向にあります。ある研究では、最適化された動線と比較して、非効率な動線では作業効率が10〜15%低下したという報告があります。
特に問題となるのが、資材の運搬や製品の搬送時の動線です。フォークリフトや台車での運搬作業において、通路幅が十分に確保されていない場合や、急な方向転換を強いられる箇所があると、作業時間が大幅に増加してしまいます。また、異なる作業者の動線が交差する場所では、安全確保のための一時停止や待機時間が発生し、それらが積み重なって大きな時間的ロスとなっています。
部署間の干渉で起こる品質管理の問題
工場内の限られたスペースに複数の工程や部署が混在することで、品質管理上の深刻な問題が発生することがあります。特に、原材料の保管場所と完成品の保管スペースが近接している場合、コンタミネーション(異物混入)のリスクが高まります。
また、異なる製品ラインが近すぎることで、作業者の勘違いや取り違えが起こりやすくなります。こうした問題は、スペースに余裕があれば防げるものですが、狭いスペースでの作業を強いられることで、品質管理の基準を維持することが困難になっているのです。例えば、ある食品製造工場では、原材料と完成品の保管スペースを明確に分離する取り組みを行いました。その結果、品質関連のクレームが前年比で約20%減少したという報告があります。
設備配置の制約による作業効率の悪化
工場内の設備配置は、単に機械を置くスペースだけでなく、メンテナンスや清掃のための作業スペースも考慮する必要があります。しかし、多くの工場では設備間のスペースが十分に確保されておらず、結果として日常的なメンテナンス作業に支障をきたしています。
特に大型の製造設備周辺では、点検や部品交換のための十分なスペースが確保されていないケースが多く見られます。その結果、通常なら30分で済む点検作業に1時間以上かかってしまったり、設備の一部にアクセスできないために問題の早期発見が遅れたりするといった事態が発生しています。また、清掃作業が行き届かないことで、設備の劣化が早まるという二次的な問題も起きています。
スペース不足が引き起こす在庫管理の課題
在庫管理の効率化には、適切な保管スペースの確保が不可欠です。しかし、多くの工場では在庫保管スペースが不足しており、それが様々な問題を引き起こしています。
まず、スペース不足により、パレットやラックを効率的に配置できず、結果として在庫の把握が困難になっています。また、急な注文や生産計画の変更に対応するための余裕スペースが確保できないため、通路に仮置きせざるを得ないケースも少なくありません。これは、作業効率の低下だけでなく、安全面でも大きなリスクとなっています。
さらに、垂直方向のスペースを有効活用できていないケースも多く見られます。天井高を活かした高層ラックの導入や、自動倉庫システムの設置により、保管効率を大幅に向上させることが可能です。例えば、ある製造業では高層ラックの導入により保管効率が約1.5倍に向上したという事例があります。しかし、多くの工場では依然として従来の平置き方式が主流となっています。
工場スペースを有効活用する3つの実践的手法
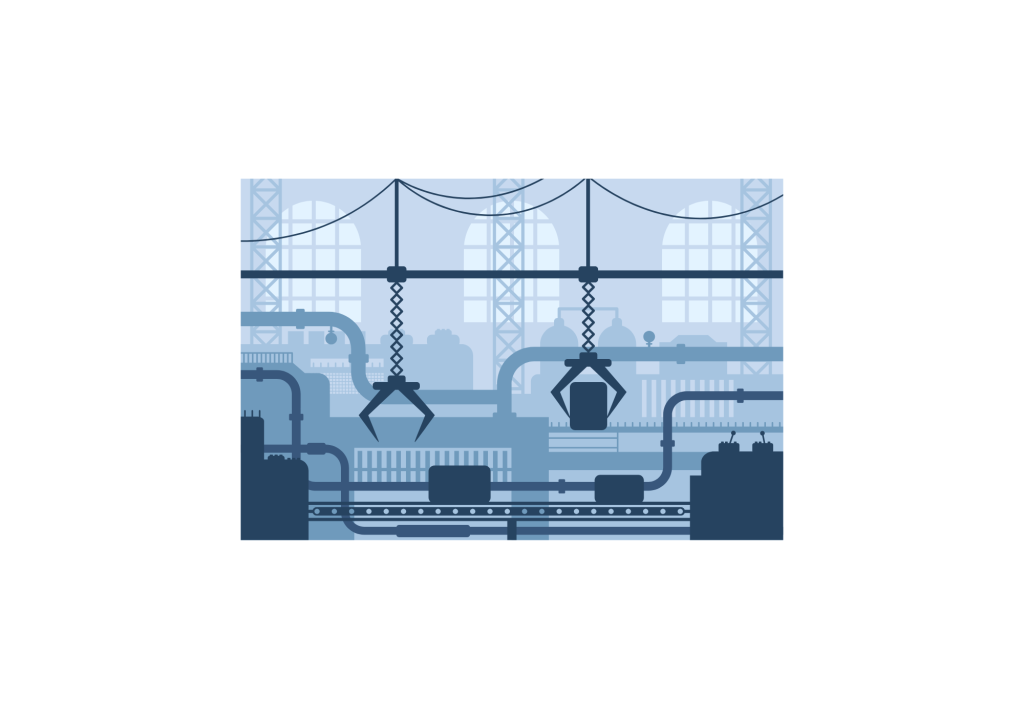
製造現場において、限られたスペースを最大限に活用することは、生産性向上の重要な鍵となっています。しかし、多くの工場では既存のレイアウトや設備配置にとらわれ、効率的な空間活用ができていないのが現状です。ここでは、工場設計のエキスパートとして30年以上の実績を持つ第一テントが、実践で効果が実証された工場スペースの有効活用法をご紹介します。これらの手法は、大規模な設備投資を必要とせず、比較的短期間で導入可能な方法ばかりです。
パーテーションによる空間の最適化
工場内の空間を効率的に区切るパーテーションの活用は、スペースの有効利用において即効性の高い解決策となっています。可動式のパーテーションを導入することで、作業内容や生産量の変化に応じて柔軟にレイアウトを変更することが可能になり、その結果として作業効率が平均20%向上したという実績もあります。
最新の工業用パーテーションは、防音性や断熱性に優れ、さらに必要に応じて透明パネルを組み込むことで、視認性を確保しながら作業空間を分離できます。これにより、異なる工程間の相互干渉を防ぎつつ、作業者の安全性も高めることができるのです。特に、品質管理が重要な製造工程では、パーテーションによる明確な区画分けが、製品の品質向上に大きく貢献しています。
動線分析に基づくレイアウト改善
効率的な工場運営には、作業者の移動距離を最小限に抑えることが不可欠です。動線分析を実施することで、無駄な移動や交差による待ち時間を削減し、作業効率を大幅に改善できます。実際の分析では、作業者の1日の移動を詳細に追跡し、頻繁に往来する地点間の距離を最短にするようレイアウトを最適化していきます。
この分析に基づくレイアウト改善では、まず作業頻度の高い工程同士を近接させ、その間の通路幅を作業内容に応じて適切に設定します。フォークリフトや台車の使用頻度が高い場所では十分な通路幅を確保し、手作業中心の区画では必要最小限の通路幅とすることで、スペースの有効活用を図ります。
上部空間の活用とメザニン設置
工場の上部空間は、多くの場合十分に活用されていない貴重なスペースです。天井高を活かしたメザニン(中二階)の設置により、床面積を実質的に増加させることが可能になります。具体的な拡大率は、工場の構造や法規制により異なります。これは、特に保管スペースや軽作業スペースの確保に効果的な手法です。
メザニンの設置においては、重量物の配置や作業者の動線、さらには建築基準法の規定にも配慮が必要になります。専門家による適切な設計と施工により、安全性と使い勝手の両立を図ることが重要です。実際の導入事例では、メザニン設置により保管効率が向上し、床面の作業スペースにも余裕が生まれたことで、生産性の向上につながった例が報告されています。
設備配置の見直しによる省スペース化
既存の製造設備の配置を見直すことで、驚くほどの空間創出が可能になることがあります。設備のコンパクト化や、使用頻度に応じた配置の最適化により、限られたスペースを最大限に活用できます。
特に注目すべきは、設備間のデッドスペースの活用です。従来は点検や修理のために確保していた余剰スペースを、可動式の作業台や工具棚として活用することで、スペース効率を高めることができます。また、設備の向きを変更するだけでも、大きな省スペース効果が得られることもあります。実例として、ある工場では設備配置の見直しにより、同じ床面積で生産能力を大幅に向上させることに成功したケースがあります。
パーテーションの活用で
工場内の空間を柔軟に区切り
作業効率と安全性を同時に向上させましょう。
製造業で成功した工場スペース改善事例
工場スペースの改善は、理論だけでなく実践においても大きな成果を上げています。第一テントでは、製造業各社の現場で実際に行われた改善事例を豊富に蓄積しており、その中から特に効果的だった取り組みをご紹介いたします。これらの事例は、それぞれの業種特有の課題を克服しながら、スペースの有効活用によって生産性の向上を実現したものばかりです。皆様の工場でも応用可能な実践的なヒントが見つかるはずです。
食品工場での衛生区画と効率化の両立
大手食品メーカーA社では、製造ラインの効率化と衛生管理の両立という課題に直面していました。特に原材料の搬入から製品の出荷までの工程で、交差汚染の防止と作業効率の向上という、一見相反する要件の解決が求められていたのです。
この課題に対し、まず清浄度に応じたゾーニングを実施。作業場を衛生区画ごとに明確に分離し、各区画間の接点を最小限に抑えました。具体的には、原材料保管エリア、製造エリア、包装エリア、出荷エリアを完全に分離。それぞれの区画をパーテーションで仕切り、人とモノの流れを一方向に制御することで、交差汚染のリスクを大幅に低減させることに成功しています。
その結果、衛生管理の向上と同時に、製品の動線が整理され、作業効率が向上しました。さらに、製品の保管スペースを最適化したことで、在庫回転率も改善されました。
機械部品工場の工程別エリア最適化
精密機械部品を製造するB社では、多品種少量生産への対応に苦心していました。従来の固定式レイアウトでは、製品の種類や生産量の変動に柔軟に対応できず、スペースの無駄が発生していたのです。
この問題に対し、工程別エリアの最適化を実施。まず、作業頻度の分析を行い、高頻度の工程を近接配置することで、部品の移動距離を最小化しました。また、可動式のパーテーションを導入し、生産品目に応じて作業スペースを柔軟に変更できる仕組みを構築。これにより、繁忙期と閑散期での空間の有効活用が可能になりました。
その結果、作業者の移動距離が削減され、生産リードタイムが短縮されました。また、フレキシブルな空間活用により、新製品の試作スペースの確保も容易になりました。
電機メーカーの組立ライン改善例
家電製品を製造するC社では、季節商品の生産変動に対応するため、組立ラインの改善が急務となっていました。特に、エアコンの需要期には作業スペースが不足し、効率的な生産に支障をきたしていました。
この課題に対し、まず天井高を活用した立体的なスペース活用を実施。部品棚を上部に配置し、使用頻度の高い部品は作業者の手の届く位置に、予備部品は上段に収納する方式を採用しました。また、組立ラインをU字型に配置することで、作業者の移動距離を最小限に抑えています。
この改善により、同じ床面積でより高い生産能力を確保しました。さらに、作業者の動線が整理されたことで、習熟期間の短縮にもつながりました。
スペース活用で実現した生産性30%向上
自動車部品メーカーD社では、従来の平置き式倉庫からの脱却を図り、垂直統合型の保管システムを導入。これにより、限られた工場スペースを最大限に活用することに成功しました。
具体的には、天井高を活かした自動倉庫システムの導入と、フォークリフトの動線を考慮した通路幅の最適化を実施。また、ピッキング場所を作業頻度に応じて配置し、出荷作業の効率化も図りました。使用頻度の高い部品は低層に、予備部品は上層に配置する方式を採用することで、作業効率と保管効率の両立を実現しています。
この改善により、保管効率が向上し、ピッキング作業時間が短縮されました。結果として、工場全体の生産性が向上する成果を上げました。
スペース有効活用のための具体的な導入ステップ
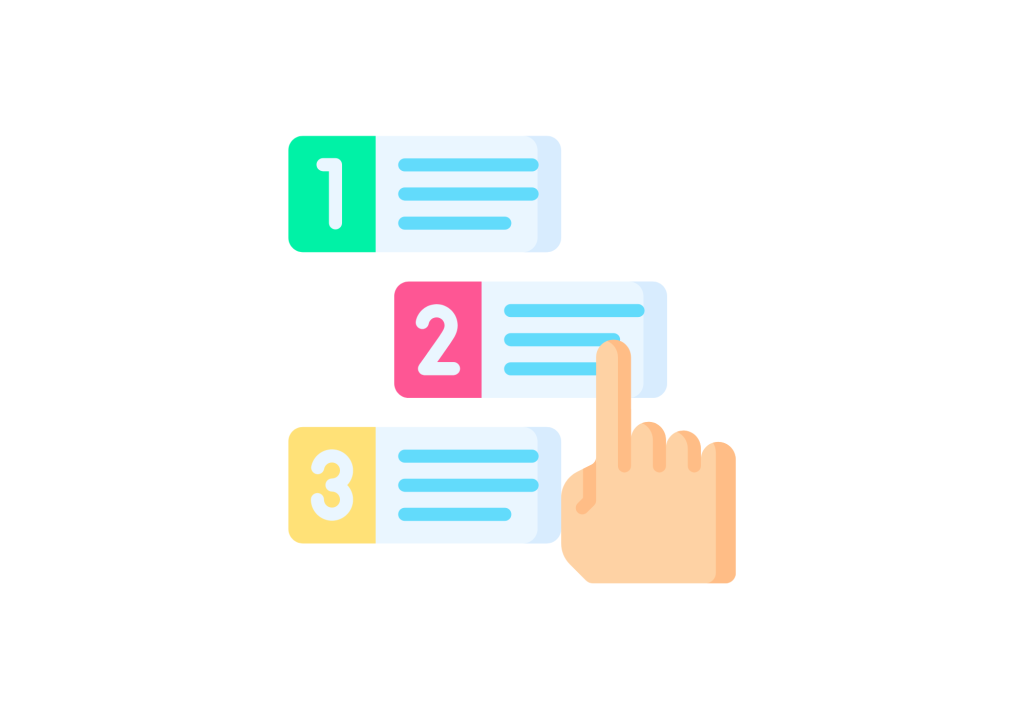
工場スペースの有効活用を実現するためには、体系的なアプローチが欠かせません。ただパーテーションを設置するだけでは、期待する効果は得られないかもしれません。ここでは、第一テントが30年以上の実績で培った工場スペース改善のノウハウをもとに、確実に成果を上げるための導入ステップをご紹介します。今すぐにでも実践可能な具体的な手順に落とし込んでいますので、ぜひ自社の工場改善にお役立てください。
現状分析と課題の明確化
効果的なスペース活用を実現するための第一歩は、現状を正確に把握することから始まります。工場レイアウト設計の経験を持つ第一テントでは、以下のような分析アプローチを提案しています。
まず、現場での詳細な動線調査を実施。作業者の移動経路や作業時間を記録し、効率化の余地がある箇所を特定していきます。具体的には、1日の作業における移動距離の計測や、作業スペース間の往来頻度の調査などを行います。この調査により、無駄な動きや非効率な空間配置が明確になるのです。
次に、設備や保管場所の使用率を分析。特に注目すべきは、時間帯や曜日による使用率の変動です。この分析により、スペースの過不足が生じている場所や時間帯が浮き彫りになります。
最適なパーテーション選びのポイント
工場の用途や目的に応じた最適なパーテーションを選定することは、スペース活用の成否を左右する重要な要素となります。材質や仕様の選定には、以下のような観点からの検討が必要です。
まず、使用環境に適した材質の選択が重要です。例えば、食品工場であれば耐水性と清掃のしやすさが求められ、機械加工工場では耐久性と防音性が重視されます。また、作業現場の視認性確保が必要な場合は、透明パネルの採用も検討すべきでしょう。
さらに、設置後の運用を見据えた可動性の検討も欠かせません。生産品目や量の変動が大きい工場では、レイアウト変更に対応できる可動式パーテーションが有効です。一方、固定的な工程が中心の工場では、より堅牢な固定式の選択が望ましいかもしれません。
予算と工期を考慮した導入計画
スペース改善プロジェクトを成功に導くためには、現実的な予算と工期の設定が重要です。工場の規模や改善内容によって異なりますが、一般的な導入計画は以下のような段階で進めていくことが考えられます。
まず、初期投資を抑えつつ確実な効果を得るため、改善を段階的に実施することをお勧めします。例えば、最初は最も効果が期待できる製造ラインから着手し、その成果を確認しながら他のエリアへと展開していく方法です。これにより、投資対効果を見極めながら、計画的な予算執行が可能になります。
工期については、製造ラインの稼働への影響を最小限に抑えるため、休日や生産調整期間を利用した施工計画を立てることが重要です。基本的なパーテーション設置の工期は、事前の準備期間を含めて工場の規模や状況によって異なりますが、一般的に数日から数週間程度かかることがあります。
効果測定と継続的な改善方法
スペース改善の効果を最大化するためには、導入後の効果測定と継続的な改善が不可欠です。具体的な評価指標としては、作業時間の短縮率、動線の効率化による移動距離の削減、スペース利用率の向上などが挙げられます。
効果測定は、定量的な指標と定性的な評価の両面から行うことが重要です。例えば、作業時間や移動距離といった数値データに加え、作業者からのフィードバックも重要な評価要素となります。これらのデータを定期的に収集・分析し、必要に応じてレイアウトの微調整や運用方法の見直しを行っていきます。
改善サイクルを継続的に実施するためには、定期的な効果測定と分析を行うことが重要です。具体的な頻度は、各工場の状況に応じて設定することが望ましいでしょう。また、生産品目や量の変動に応じて、パーテーションの配置や使用方法を柔軟に見直していく姿勢も重要です。
まとめ
- 工場スペースの非効率な活用は、作業動線の混乱、品質管理の問題、設備メンテナンスの困難さ、在庫管理の非効率化など、多岐にわたる課題を引き起こす
- パーテーションによる空間の最適化、動線分析に基づくレイアウト改善、上部空間の活用とメザニン設置は、大規模な設備投資を必要とせず即効性の高い改善策である
- 食品、機械部品、電機メーカーなど、業種を問わず適切なスペース活用により、生産性の向上、品質管理の改善、作業効率の向上などの具体的な成果が得られている
- スペース改善の成功には、現状分析による課題の明確化、用途に応じた適切なパーテーションの選定、計画的な導入、継続的な効果測定が不可欠である
工場スペースの有効活用は、企業の競争力を高める重要な経営課題です。第一テントでは、30年以上にわたる実績と専門知識を活かし、お客様の工場に最適なスペース改善プランをご提案いたします。まずは現状の課題や目標についてお聞かせください。専門スタッフが丁寧にご相談に応じさせていただきます。
工場スペースの最適化で生産性を向上させませんか?
第一テントでは、多くの企業様のスペース活用を
サポートしてきました。
成功事例をご覧いただき
貴社の工場改善にお役立てください。
お問い合わせはこちら
・工場向け高速シートシャッターの全ガイド:メリット、デメリット、選び方
・工場向けシートシャッター修理のすべて:故障原因とプロがすすめる修理・メンテナンス・補修サービスの紹介 |